- Введение
- Продукция
- Маркировка
- Функции
- Руководство пользователя
- О документации
- Меры безопасности
- Индикация
- Максимальная конфигурация
- CAN-топология
- Подключение CAN-шины
- Разъемы и провода
- Монтаж модулей
- Общие правила и нормы эксплуатации
- Технические характеристики
- Условия эксплуатации
- Использование по назначению
- Маркировка
- Техническое обслуживание
- Транспортирование и хранение
- Упаковка
- Гарантийные обязательства
- Обновление
- Платформа CAN bp.
- CANopen
- ISOBUS (ISO 11783)
- Решения
- Исследования
- Параметризация
- Программирование
- Литература и источники
- Образование
- Дополнительная информация
- Цифровые решения для современного сельского хозяйства
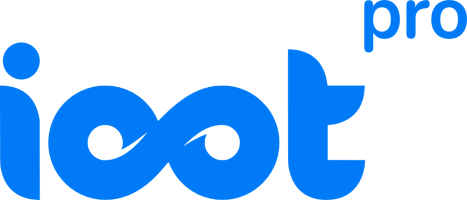
Робот манипулятор¶
Современные тенденции в производстве, такие как увеличение производительности труда, ускорение вывода на рынок новой продукции и индивидуальные заказы, требуют новых принципов и подходов к производству и оборудованию. В долгосрочной перспективе промышленным предприятиям будет сложно выжить в условиях глобализации без способности быстро и гибко адаптироваться к меняющимся требованиям рынка и клиентов. Новые подходы и принципы необходимы, но их реализация требует новых технологий. Реконфигурации на аппаратном и программном уровнях управления являются одним из таких решений. Необходим переход от централизованно управляемых и сильно связанных производственных систем к модульной, распределенной системе автономных единиц. Здесь описывается концепция децентрализованного управления для реконфигурации манипулятора с шестью степенями свободы. Это демонстрация возможностей платформы CAN bp.
1. Предпосылки¶
Производственные системы, основанные на самых современных технологиях, не отвечают вышеуказанным требованиям к более гибким производственным технологиям. Обрабатывающая промышленность в основном использует в производстве портфель специализированных производственных систем (DMS) и гибких производственных систем (FMS). DMS характеризуются высокой производительностью, но недостаточной гибкостью. Эта производственная система адаптирована к конкретному продукту, и внедрение новых продуктов практически невозможно. Таким образом, DMS во многих случаях представляет проблему, когда жизненный цикл производства соответствующего продукта подходит к концу. FMS характеризуется высокой гибкостью, но также и высокими затратами из-за дорогостоящего оборудования, что препятствует ее широкому внедрению. Обе производственные концепции в основном управляются с использованием централизованных подходов, основанных на программируемом логическом контроллере (ПЛК) и технологии компьютеризированного числового управления (ЧПУ).
С другой стороны, адаптивная система включает производственные мощности, способные подстраиваться под колебания спроса на продукцию, адаптироваться под новые функции продукта и предназначенные для модернизации при помощи новых технологических процессов согласно меняющимся спецификациям продукции и государственным нормативам. Существующие системы, даже так называемые “гибкие” производственные системы, такими характеристиками не обладают. Новая производственная парадигма под названием “реконфигурируемые производственные системы” (RMS) определит положение производственных предприятий в XXI веке и далее. Целью RMS является создание систем, станков и управляющих средств, которые будут экономически эффективными, и смогут быстро приспосабливаться к изменениям спроса на рынке и продукции. Методики систематического проектирования и ускоренного расширения RMS представляют собой основу этой новой производственной парадигмы. Новая реконфигурируемая производственная система обеспечивает необходимую функциональность и продуктивность.
2. Реконфигурируемая рука робота¶
2.1 Механическая установка¶
Робот-манипулятор, который будет использоваться в этой демонстрации, представляет собой модульный реконфигурируемый робот-манипулятор, состоящий из IMC, как показано на рис. 1. Робот состоит из шести отдельных шарниров (т.е. IMC). Они соединены друг с другом с помощью специальных соединительных элементов (желтые элементы на рис. 1).
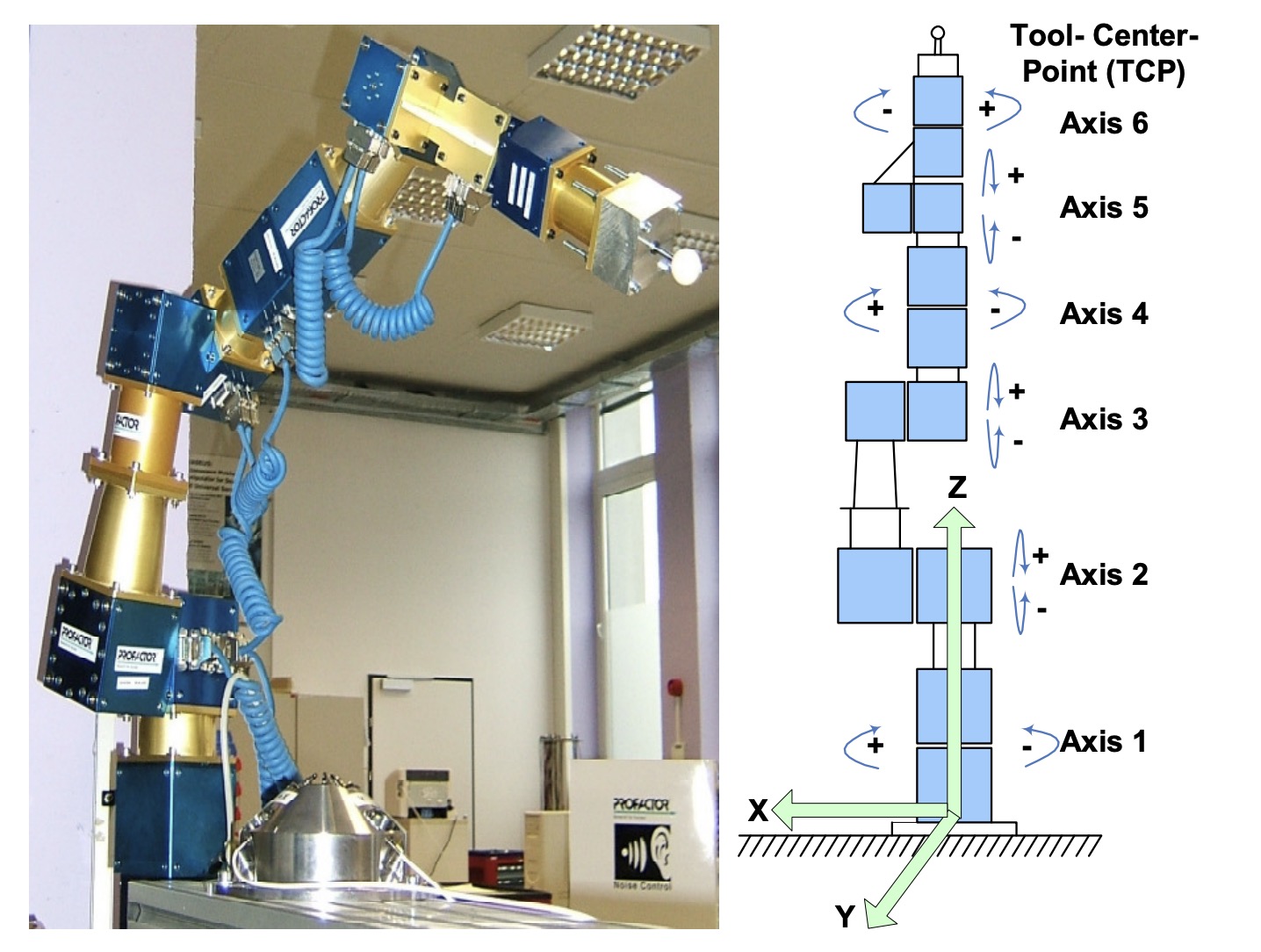
Рисунок 1: Внешний вид руки робота с 6ю степенями свободы.¶
2.2 Мехатронные компоненты¶
Шарниры IMC, можно легко применять для производственных и сборочных задач, требующих быстрой и гибкой адаптации процессов. На Рисунке 1. показаны шесть осей соединения.
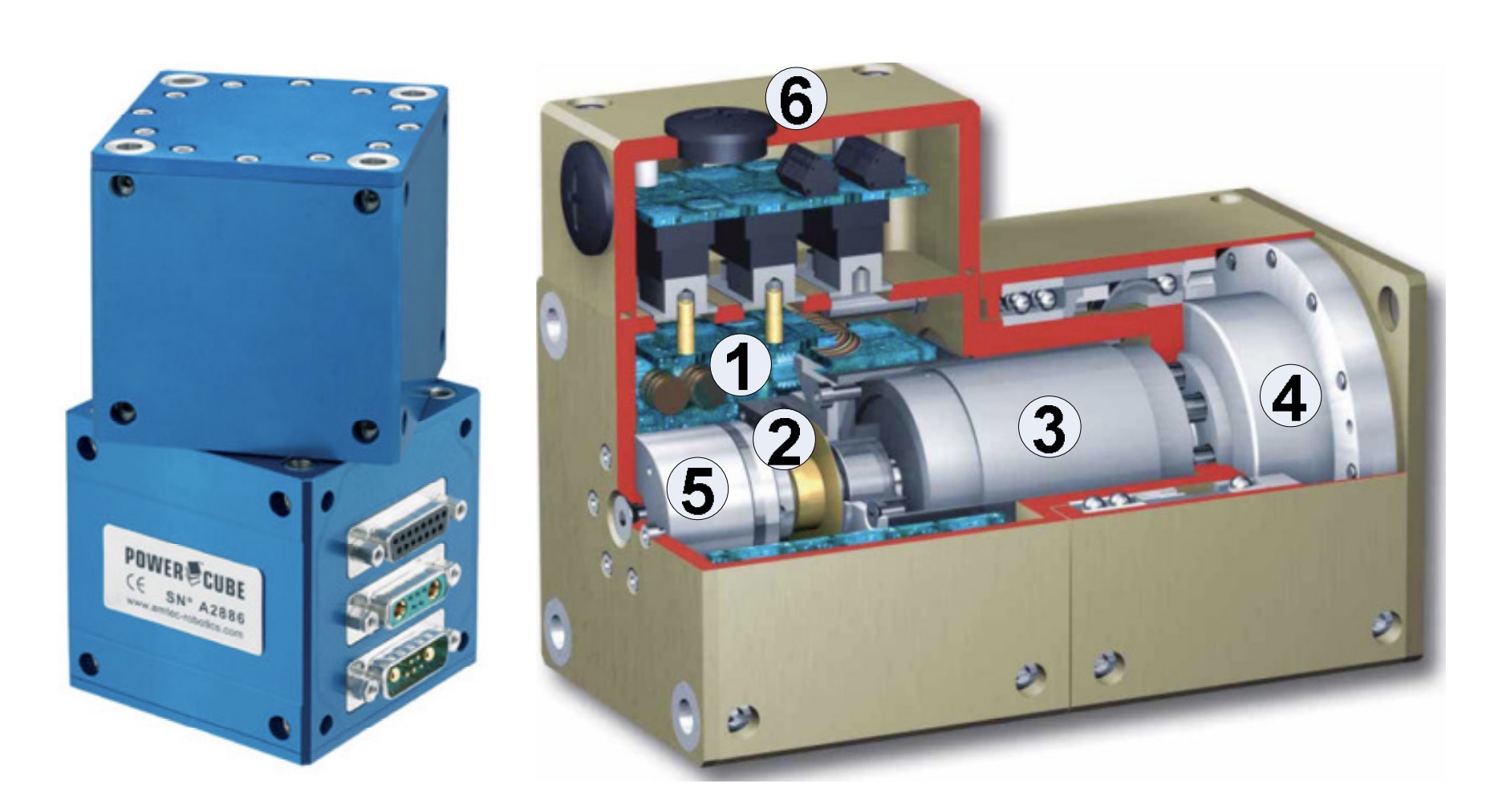
Рисунок 2: Мехатронные компоненты коленного узла робота.¶
В следующем списке приведено краткое описание функциональных возможностей:
Бесщеточный серводвигатель с гармонической приводной головкой позволяет использовать его для роботизированных задач,
Инкрементальный энкодер для управления позиционированием и скоростью,
Контроль концевых выключателей, напряжения, тока и температуры,
Встроенные опорные и концевые выключатели,
Магнитный тормоз,
Выход сигнала внутреннего энкодера,
Вход сигнала внешнего энкодера.
На рис. 2 показаны внутренние компоненты шарнира:
Электроника со встроенным блоком управления и усилителем,
Энкодер для измерения фактического положения,
Электродвигатель для высоких крутящих моментов,
Гармонический привод с передаточным отношением 161:1,
Прерыватель для удержания фактического положения в случае остановки или потери мощности,
Покрытие.
Робот, используемый для демонстрации, состоит из трех различных модулей. Оси 1 и 2 относятся к типу PR-110, оси 3 и 4 - к типу PR-90, а оси 5 и 6 - к типу PR 70. Кроме того, в таблице 1 приведен обзор конкретных параметров, которые устанавливаются для различных блоков питания в реконфигурируемом манипуляторе робота.
Параметры |
PR-70 |
PR-90 |
PR-110 |
---|---|---|---|
Номинальный крутящий момент |
0,181 Нм |
0,558 Нм |
1,1 Нм |
Максимальный крутящий момент |
0,568 Нм |
1,6 Нм |
3,3 Нм |
Напряжение |
24 ± 1 В |
24 ± 1 В |
24 ± 1 В |
Макс. ток |
15 А |
30 А |
30 А |
Рабочий крутящий момент |
23 Нм |
72 Нм |
142 Нм |
Максимальный крутящий момент |
73 Нм |
206 Нм |
425 Нм |
об/мин |
5000 мин |
4300 мин |
4500 мин |
Встроенные микроконтроллеры обеспечивают различные функциональные возможности для управления двигателями (например, половина, поворот, остановка и т.д.). Для управления каждой оси мы возьмем отдельный контроллер. Контроллер оси будет отвечать за управление положением и скоростью каждого модуля. Для связи с контроллером предусмотрены следующие интерфейсы:
Сеть зоны управления (CAN)
Внешнее подключение Ethernet
3. Модель робота и архитектура управления¶
3.1 Динамическая модель робота¶
Чтобы получить концепцию управления роботом, рассчитывается модель робота. Таким образом, кинематическая модель основана на кинематической цепи, как показано на рис. 1. Робот состоит из последовательной кинематической цепи с 6-ступенчатой передачей через модульную сборку на базе шарниров.
Чтобы рассчитать положение и ориентацию конечной точки работа (центральной точки инструмента - TCP) в декартовой системе координат и в объединенной системе координат PowerCubes, были рассчитаны прямая и обратная кинематика. Для робота с 6-ступенчатой передачей и центральным захватом на последнем шарнире решение для обратной кинематики может быть рассчитано аналитически.
Без центрального захвата или с коэффициентом усиления более 6, решение для обратной кинематики может быть рассчитано только с использованием алгоритма аппроксимации. Для сравнения, алгоритм аппроксимации Ньютона также использовался для расчета обратной кинематики. Оказалось, что аналитический способ может быть рассчитан быстрее, чем аппроксимационный. Поэтому в этой демонстрации был использован первый. Для вычисления уравнения движения
с вектором обобщенных модульных координат q, матрицей массы робота M, гироскопической матрицей G и вектором обобщенных сил Q использовались проекционные уравнения.
3.2. Модель двигателя¶
Крутящий момент, создаваемый для каждой оси робота, генерируется двигателем постоянного тока. Для расчета модели двигателя была использована эквивалентная принципиальная схема двигателя постоянного тока с постоянным возбуждением. На рис. 3 показан электрический эквивалент двигателя постоянного тока.
Результирующий крутящий момент Power Cube, включая передаточное отношение гармонического привода, может быть рассчитан в соответствии со следующим уравнением (по небрежности - полное сопротивление двигателя L A).:
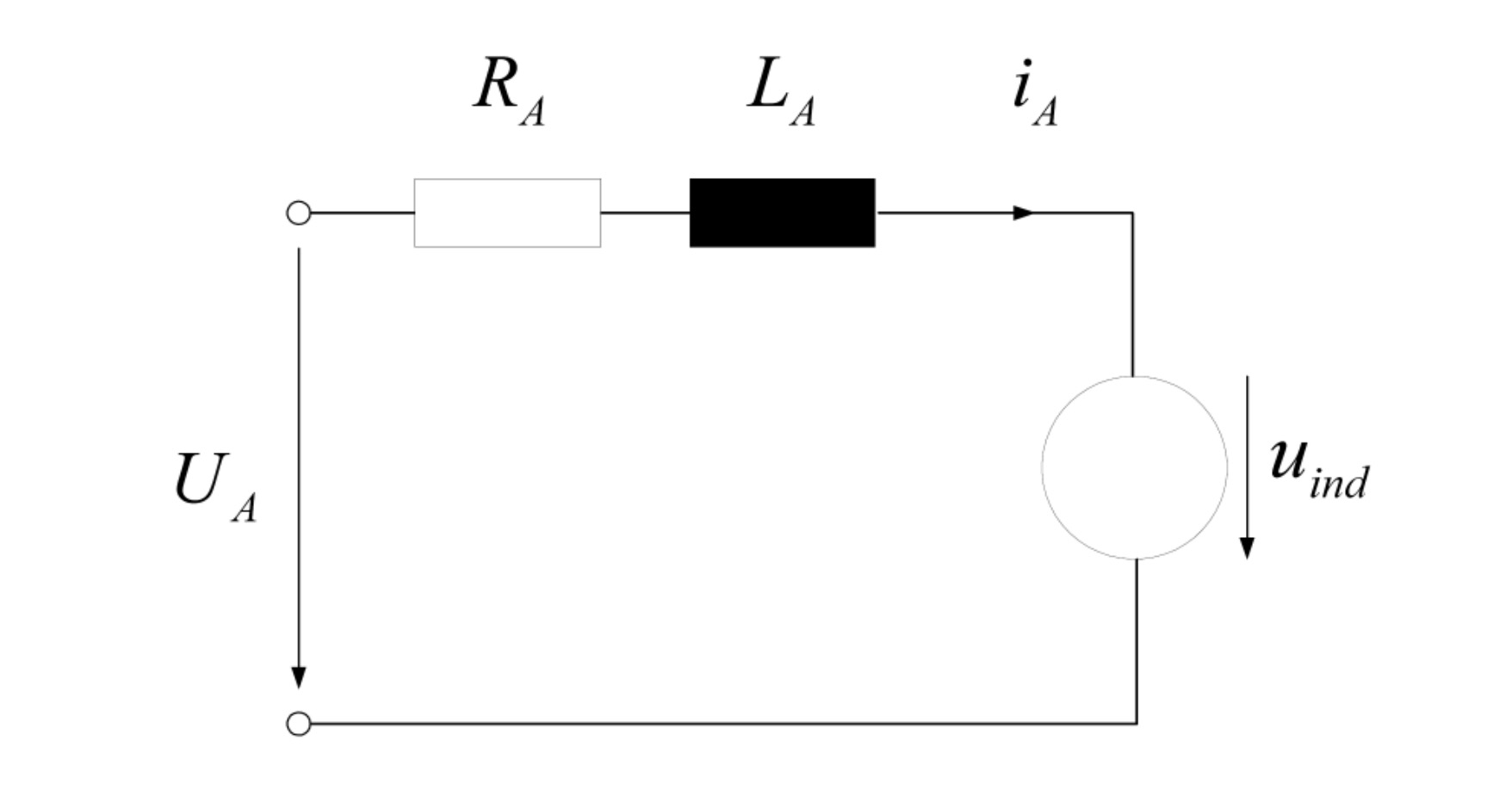
Рисунок 3: Эквивалентная принципиальная схема двигателя постоянного тока с постоянным возбуждением.¶
Где:
M PC - Крутящий момент (на оси двигателя, включая шестерню),
k m - Коэффициент пропорциональности крутящего момента двигателя и тока двигателя (M = k:sub:m`i:sub:`A)
U A - Напряжение двигателя, и
i G - Передаточное число.
3.3. Концепция управления¶
Концепция управления модульным, реконфигурируемым роботом 6-DOF показана на рис. 4.
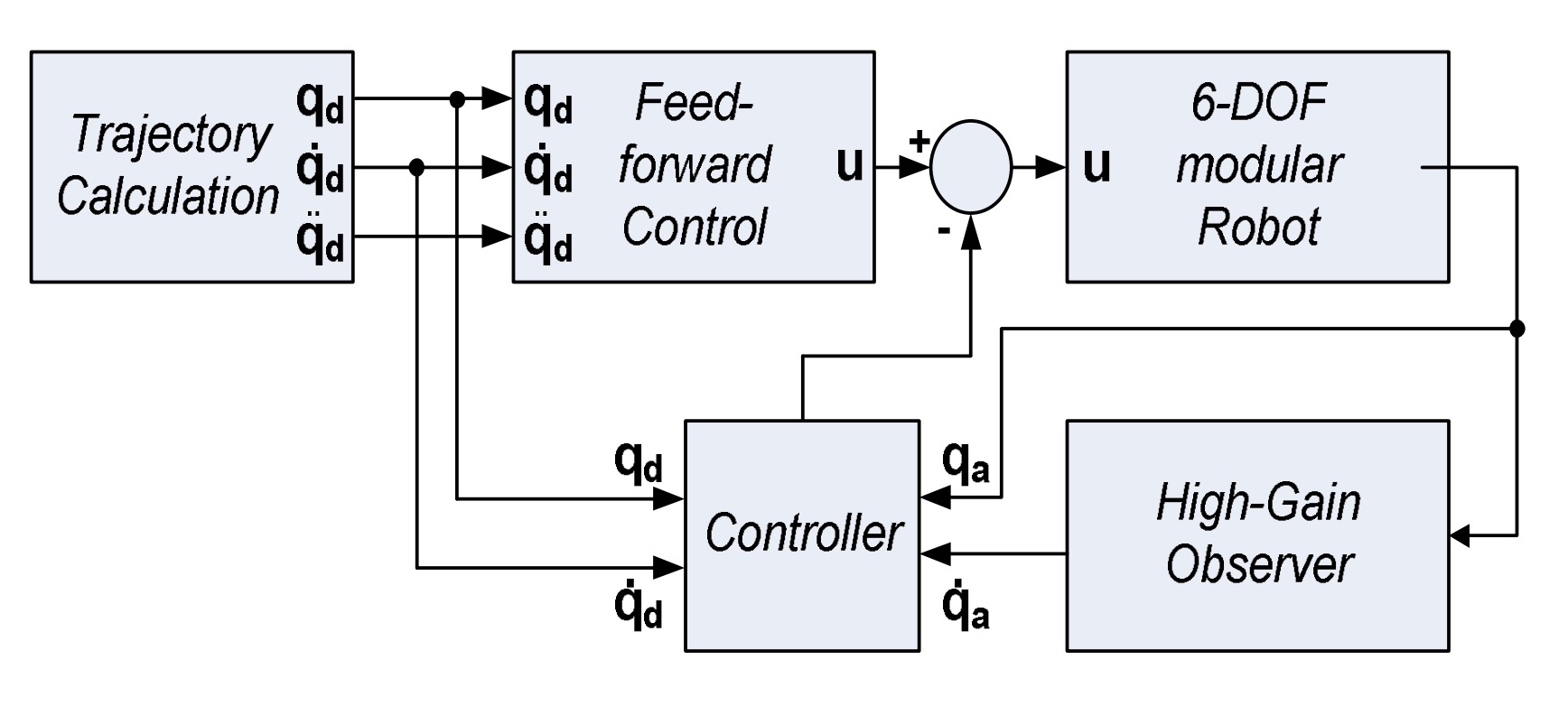
Рисунок 4: Концепция управления¶
Целью концепции управления является перемещение инструмента робота по интерполированной траектории из выбранной точки A в точку B. Движение робота должно быть плавным. Для формирования траектории был применен профиль ускорения на основе sin 2 (см. рис. 5). Блок расчета траектории на рис. 4 вычисляет желаемое угловое положение q, желаемую скорость q . и желаемое ускорение q .. для каждого модуля шарнира.
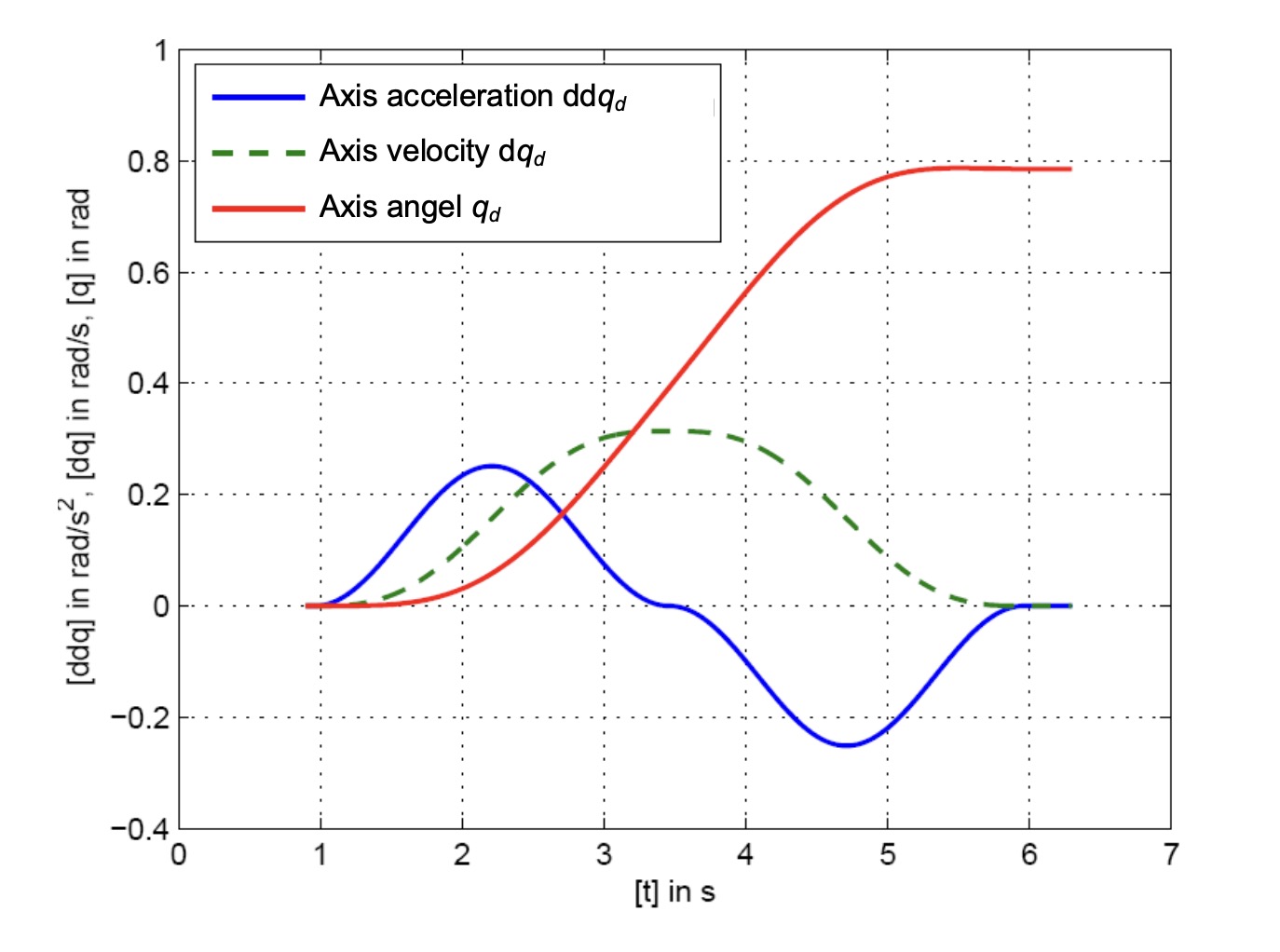
Рисунок 5: Траектория с профилем ускорения, основанным на sin 2.¶
Это приводит к определению термина «обратная связь» в концепции управления:
Для термина управления с обратной связью (т.е. контроллера робота) используется подход управления PD. Траектория в используемом законе управления включает угловое положение и угловую скорость соединений (шарниров). В результате получается следующий контроллер PD (параметры контроллера K P и K D):
с помощью q d задается желаемое положение, а q a - фактическое положение соединений.
Поскольку каждый силовой шарнир оснащен только датчиком для измерения его углового положения, прямое измерение угловой скорости невозможно. Но для концепции пользовательского управления необходимо знать угловую скорость каждого силового шарнира.
Для вычисления угловой скорости используется метод «High gain observer». Этот подход является общим для механических конструкций, поскольку в нем используется уравнение движения. На рис. 4 показана концепция управления, включающая «Observer» с высоким коэффициентом усиления для вычисления угловой скорости каждого блока на основе углового положения.
4. Концепция распределенного управления¶
4.1. Настройка встроенного оборудования и программного обеспечения¶
На рис. 6 показана аппаратная настройка (встроенное управление) реконфигурируемой роботизированной системы. Соответственно, две оси робота управляются ПК PC/104, оснащенными сопроцессором с Ethernet и модулем на платформе CAN bp для реального времени.
Вся концепция управления роботом, описанная в главе 3, реализована в функциональных блоках стандарта IEC 61499 для поддержки повторного использования и реконфигурации на уровне функциональных блоков. Среда выполнения, совместимая с IEC 61499, установлена на каждом из контроллеров PC/104 и используется для выполнения приложения управления функциональным блоком IEC 61499.
Обмен данными между PC/104 и шарниром осуществляется через CAN. Компьютер для проектирования и визуализации подключен через стандартный Ethernet к контроллерам PC/104.
Разработка программы управления роботом по стандарту IEC 61499 осуществляется с помощью IDE 4 DISC. Визуализация и HMI также моделируются с помощью функциональных блоков IEC 61499. Между SCADA и PC/104 связь по протоколу MQTT.
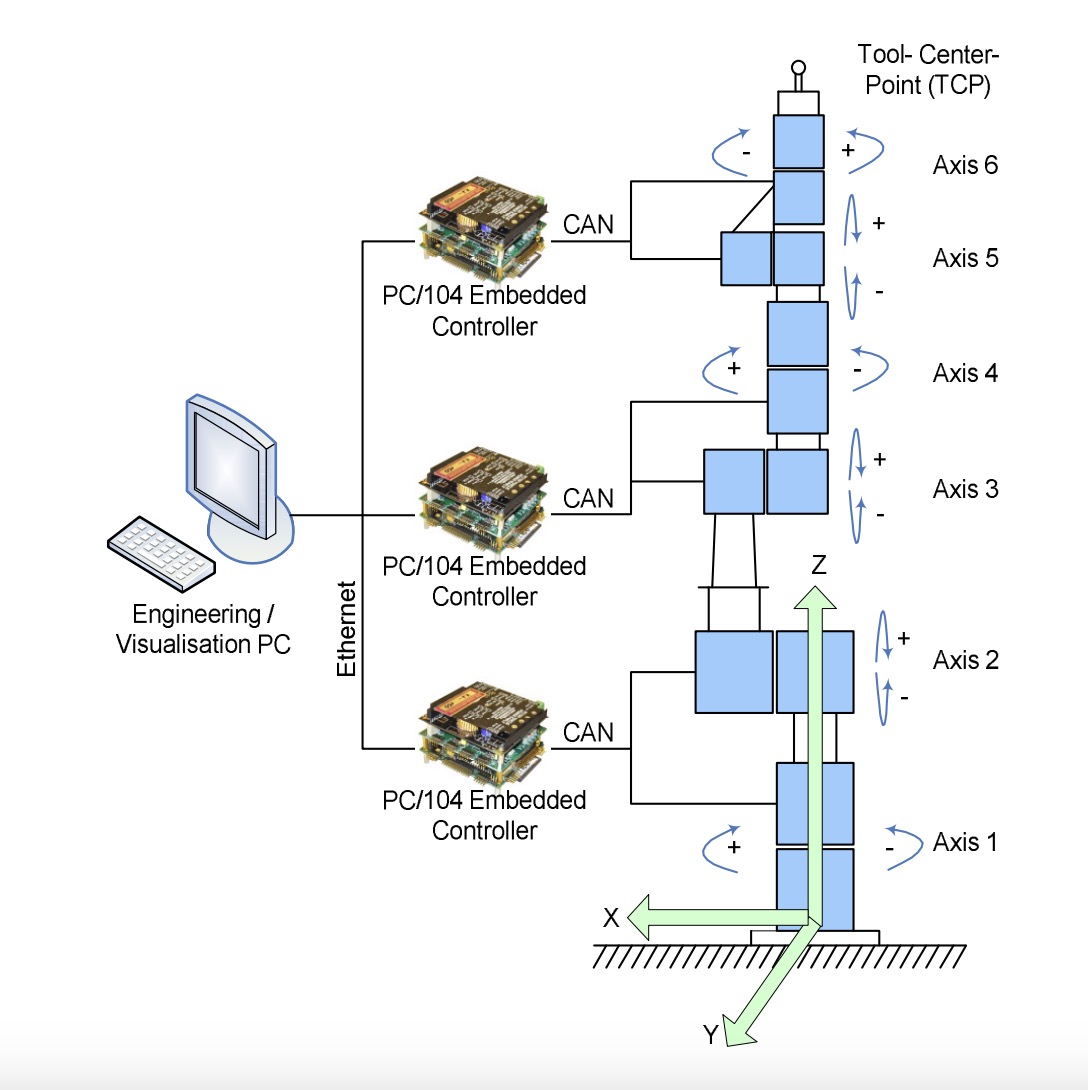
Рисунок 6: Настройка встроенного оборудования¶
4.2. Реализация распределенного управления¶
Представленная выше концепция управления (см. рис. 4) и выбранная аппаратная структура модульного робота 6- DOF (как показано на рис. 6) приводят к конфигурации системы IEC 61499, представленной на рис. 7.
Были разработаны следующие два отдельных приложения IEC 61499:
Приложение для управления роботом (RCA)
Приложение для управления HMI роботом (RHA)
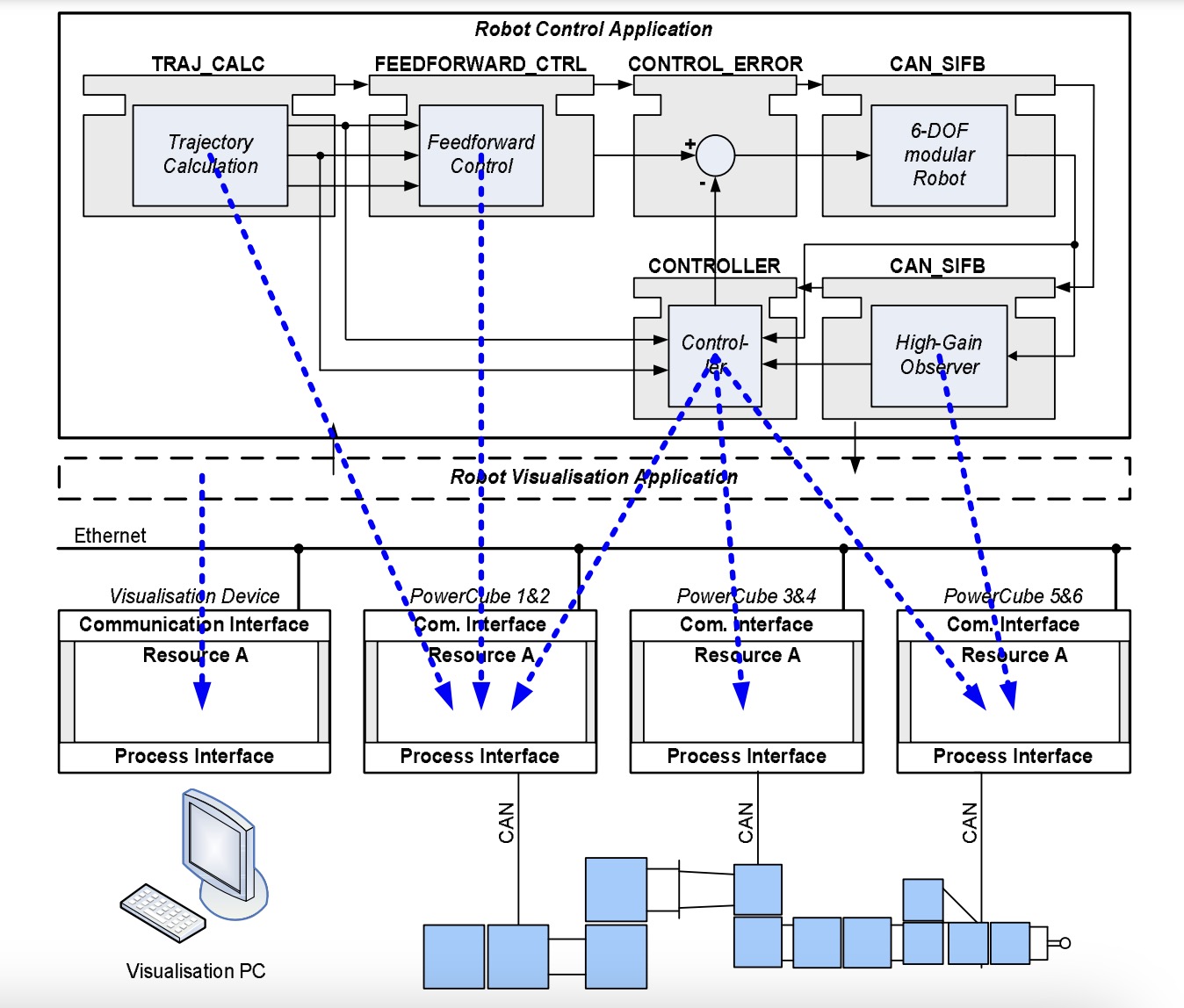
Рисунок 7: Конфигурация системы IEC 61499 для реконфигурируемого манипулятора робота с 6 степенями свободы¶
RCA содержит реализованную концепцию управления в виде приложения стандарта IEC 61499. У каждого компонента концепции управления есть свой собственный функциональный блок стандарта IEC 61499 (например, TRAJ_CALC, FEED_FORWARD_CTRL и т. д.).
Для решения вопросов визуализации и параметризации разработан специальный инструмент. RHA так же построен на базе специальной функции сервисного интерфейса человеко-машинного интерфейса по стандарту IEC 61499 блоки (SIFB). Два приложения взаимодействуют между собой с помощью функциональных блоков публикация/подписка.
Модель системы IEC 61499 для управления роботом состоит из четырёх различных удалённых устройств. Одно удалённое устройство выполняется на компьютере для визуализации (с установленным FBDK). Остальные три устройства выполняются на встраиваемом оборудовании PC/104 (с установленным FORTE). Взаимодействие между всеми устройствами происходит через Ethernet. Все RHA отображаются на устройстве для визуализации, в то время как расчёт траектории и составные функциональные блоки прямого управления (CFBD) отображаются на шарнирах 1 и 2.
CFB Observer с высокой степенью усиления подключён к шарнирам 5 и 6. Остальные модули управления (CAN SIFB и контроллер) представлены в виде вспомогательных приложений и распределены между тремя шарнирами.
4.3 Библиотека управления движением¶
Для обеспечения взаимодействия встраиваемых контроллеров и шарнирных модулей была разработана библиотека управления движением, основанная на стандарте IEC 61499 (пример изображён на рис. 8). Описание интерфейса функциональных блоков управления движением основано на спецификации управления движением ассоциации PLCopen
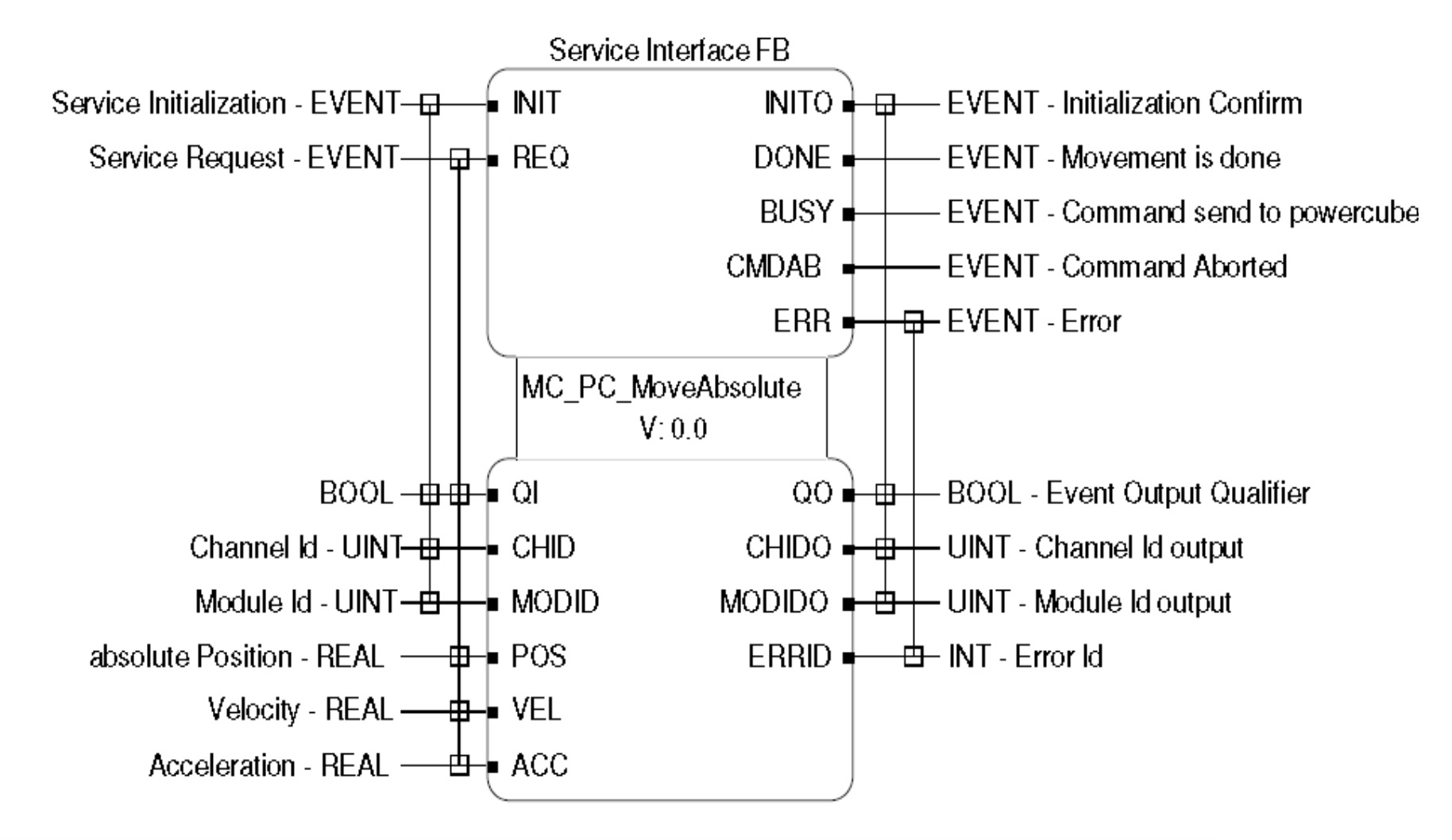
Рисунок 8: IEC 61499 Блок управления абсолютным перемещением.¶
5. Резюме и выводы¶
В данной статье обсуждалась важность применения реконфигурируемых систем в производстве. В качестве примера были представлены платформы (реконфигурируемый манипулятор робота) демонстрирующие преимущества таких систем.
Кроме того, в статье описана концепция управления роботом, которую можно применить к различным встроенным системам. Для реализации концепции децентрализованного управления использовался стандарт IEC 61499. Аппаратная часть распределённой системы управления состоит из встраиваемых контроллеров PC/104 с операционной системой Linux реального времени.
Вместе со сменными блоками манипулятора-робота и распределённой системой управления, базирующейся на стандарте IEC 61499, становится легко изменять конфигурацию реконфигурируемой роботизированной системы (то есть возможна настройка как аппаратной, так и программной частей).